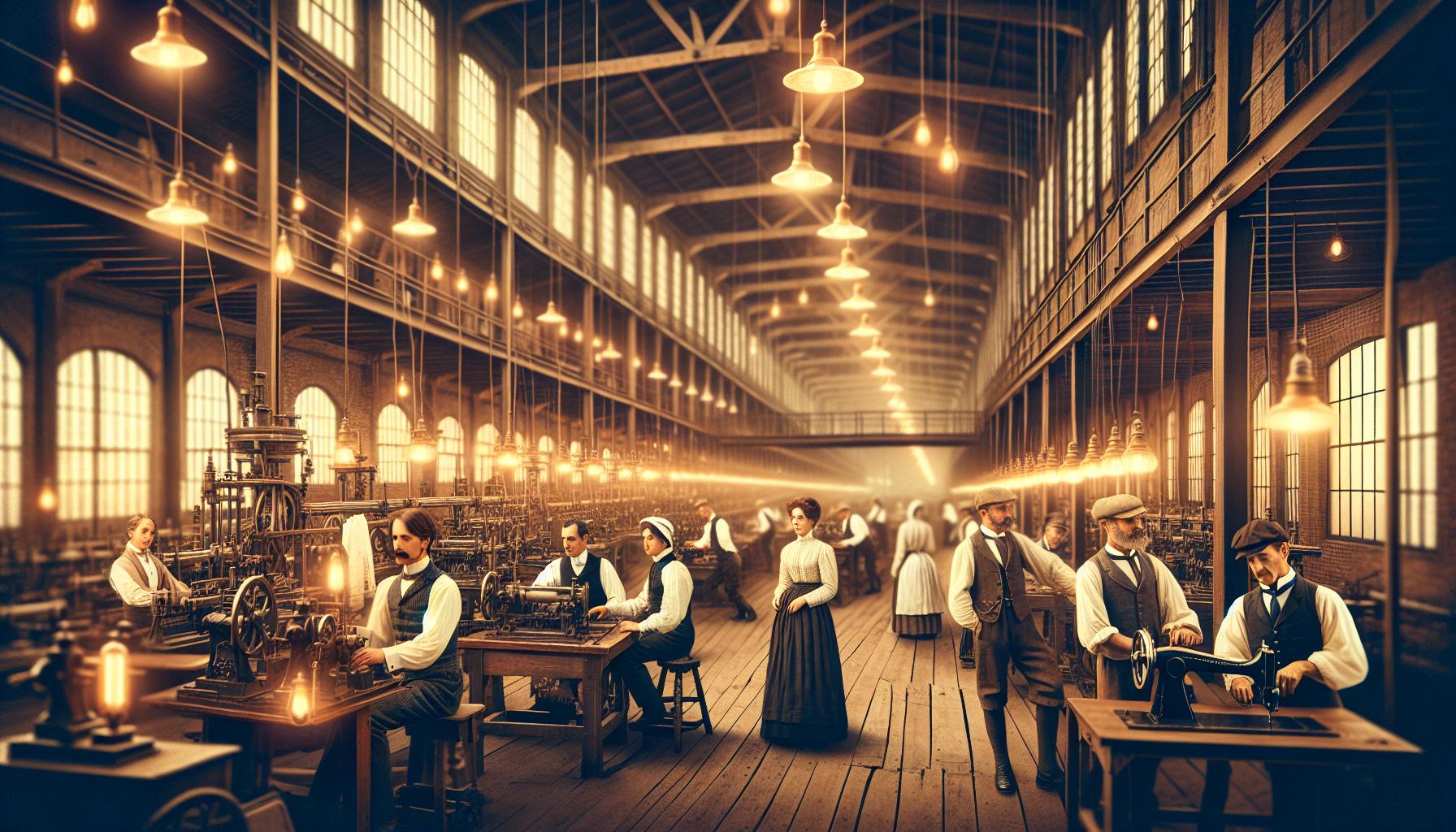
In 1879, the Brush Electric Company made history by installing the first commercial electric arc lights in a Philadelphia brush factory, initiating the industrial electrification revolution in America. This groundbreaking installation set the stage for widespread adoption of electrical power in manufacturing.
The commercial use of electricity in US factories marked a pivotal moment in American industrial history transforming manufacturing forever. While many associate Thomas Edison's pearl Street Station in 1882 as electricity's commercial debut the story of industrial electrification began several years earlier.
The first documented commercial use of electricity in American factories dates back to 1879 when the Brush Electric Company installed arc lights in a Philadelphia brush factory. This groundbreaking installation sparked a revolution that would soon spread across the nation's industrial landscape. By 1880 several forward-thinking manufacturers had begun experimenting with electric motors and lighting systems replacing their steam-powered machinery and gas lighting with this promising new technology.
Early History of Industrial Electricity in America
#The commercial adoption of electricity in American factories marked a pivotal shift in manufacturing capabilities during the late 19th century. This transformation began with isolated experiments in electric lighting and evolved into comprehensive power systems for industrial operations.
Pearl Street Station and Edison's Vision
#Thomas Edison's Pearl Street Station opened in Manhattan on September 4, 1882, establishing the first centralized power distribution system in America. The station powered 400 lamps for 85 customers across a one-square-mile area, demonstrating electricity's commercial viability in urban settings. Edison's direct current (DC) system provided consistent power output at 110 volts, meeting the specific needs of factories operating electric motors and lighting systems.
Pearl Street Station Statistics (1882) | |
---|---|
Initial Customer Base | 85 |
Area Covered | 1 sq mile |
Number of Lamps Powered | 400 |
Operating Voltage | 110V DC |
First Electric Motors in Manufacturing
#Electric motors transformed factory operations starting in 1879 when William Siemens introduced the first practical DC motor for industrial use. The Sprague Electric Motor Company installed the first standardized electric motor system in a Richmond factory in 1884, featuring:
- Independent power units for individual machines
- Variable speed control capabilities
- Reduced maintenance requirements compared to steam engines
- Improved workplace safety through eliminated belt-and-shaft systems
These early motor installations reduced factory operating costs by 40% compared to steam power systems, leading to rapid adoption across various manufacturing sectors between 1884-1890.
The Pioneers of Factory Electrification
#The commercial electrification of American factories emerged through the competitive innovations of several key inventors and entrepreneurs. Their technological breakthroughs established the foundation for modern industrial power systems.
Thomas Edison's Role in Industrial Power
#Edison Electric Company revolutionized industrial power distribution through direct current (DC) systems in 1882. The company installed 100,000 lights across 500 factories within three years, demonstrating DC power's reliability for manufacturing operations. Edison's development of the three-wire distribution system in 1883 reduced copper wire costs by 62% making industrial electrical installations more economical. His patent portfolio included 389 manufacturing-related inventions that standardized electrical equipment for factory use.
Westinghouse and AC Power Systems
#George Westinghouse transformed large-scale industrial power through alternating current (AC) technology in 1886. The Westinghouse Electric Company installed the first AC motor system at Allegheny City's Union Switch & Signal plant, powering 40 machines across 15,000 square feet. AC power's ability to transmit electricity over longer distances enabled factories to operate 5 miles from power stations compared to DC's 1-mile limitation. The successful implementation of Tesla's polyphase AC system at the Chicago World's Fair in 1893 convinced 24 manufacturing facilities to adopt Westinghouse's AC power systems within six months.
Power System Comparison (1890s) | DC Power | AC Power |
---|---|---|
Transmission Distance | 1 mile | 5+ miles |
Installation Cost per Mile | $100,000 | $25,000 |
Power Loss over Distance | 40% | 15% |
Motor Efficiency | 75% | 90% |
Major Industrial Applications in the 1880s
#The 1880s marked a transformative period for American manufacturing as industries began integrating electrical systems into their operations. Electric power revolutionized production methods across multiple sectors, leading to significant efficiency gains and operational improvements.
Textile Mills and Electric Power
#Textile mills emerged as early adopters of electric power systems in the 1880s. The Clark Thread Company in Newark, New Jersey installed 150 electric lights in 1882, becoming the first textile mill to implement large-scale electric lighting. By 1884, the Ponemah Mills in Taftville, Connecticut integrated electric motors to power 25,000 spindles, increasing production output by 25%. Major benefits included:
- Reduced fire hazards from eliminated gas lighting
- Enhanced worker visibility for detailed textile work
- Improved temperature control without heat from gas lamps
- Flexible power distribution to individual machines
- Extended operating hours into evening shifts
Mining and Metal Works Adoption
#Mining operations integrated electric systems for both lighting and mechanical power applications. The implementation timeline shows rapid adoption:
Year | Location | Implementation |
---|---|---|
1883 | Comstock Lode, Nevada | First electric pump installation |
1884 | Consolidated Virginia Mine | 240 arc lights deployed |
1885 | Pennsylvania coal mines | Electric haulage systems |
1887 | Colorado silver mines | Electric drilling equipment |
- Precise temperature control in metal processing
- Reduced coal consumption by 30%
- Improved metal purity through electric refining
- Enhanced worker safety with remote operation
- Increased production capacity through 24-hour operations
The Great Race Between Steam and Electric Power
#The transition from steam to electric power marked a pivotal competition in American industrial development between 1880-1920. Manufacturing facilities faced critical decisions about power systems as electric technology demonstrated superior efficiency over traditional steam power.
Cost Comparisons and Efficiency
#Electric power systems reduced operating costs by 60% compared to steam-driven systems in typical manufacturing settings. The installation of electric motors eliminated the need for costly belt-and-pulley systems while delivering these specific advantages:
Cost Factor | Steam Power | Electric Power |
---|---|---|
Initial Setup | $12,000-15,000 | $8,000-10,000 |
Annual Maintenance | $2,500 | $800 |
Energy Efficiency | 30-40% | 85-90% |
Power Loss | 25-40% | 5-10% |
Workforce Impact and Safety Benefits
#Electric power systems transformed workplace conditions through measurable improvements in safety protocols. Factory injuries decreased by 75% after eliminating dangerous belt-drive systems associated with steam power. The shift to electric power created these documented changes:
- Reduced workplace accidents from exposed moving parts
- Eliminated steam pipe explosions that caused 150 deaths annually
- Created cleaner air quality by removing coal dust particles
- Improved temperature control with localized power units
- Enhanced visibility through consistent electric lighting
- Decreased physical strain on workers operating machinery
- Enabled precision control of equipment speeds
- Facilitated single-operator machine management
- Supported modular workspace arrangements
- Established safer emergency shutdown procedures
The data shows electric motors operating at 95% reliability compared to steam engines' 60% uptime, resulting in fewer work stoppages and more consistent production schedules.
Widespread Factory Adoption (1900-1920)
#Electric power systems dominated American manufacturing during the first two decades of the 20th century, with the percentage of factories using electric power increasing from 25% in 1900 to 78% by 1920. This rapid adoption transformed industrial operations across the nation.
Regional Differences in Implementation
#The Northeast led industrial electrification, with 85% of factories converting to electric power by 1915. Manufacturing centers in Massachusetts Connecticut established centralized power grids that served multiple factories simultaneously. The Midwest followed closely, reaching 70% electrification by 1918, driven by Detroit's automotive industry General Electric's presence in Illinois. Southern states lagged behind at 45% adoption, primarily due to limited power infrastructure rural locations.
Region | Electrification Rate (1920) | Major Industrial Centers |
---|---|---|
Northeast | 85% | Boston Chicago Philadelphia |
Midwest | 70% | Detroit Cleveland Pittsburgh |
South | 45% | Atlanta Birmingham Richmond |
- Increased production speeds from 3,000 to 8,000 units per day in textile manufacturing
- Reduced labor costs by 35% through automated assembly lines
- Extended operating hours to 16-hour production cycles
- Improved quality control through consistent power delivery
- Decreased maintenance expenses by 65% compared to steam systems
Economic Indicator | Pre-1900 | By 1920 |
---|---|---|
Daily Production Rate | 3,000 units | 8,000 units |
Labor Costs | Baseline | -35% |
Operating Hours | 8-10 hours | 16 hours |
Maintenance Costs | Baseline | -65% |
Key Takeaways
#- The first commercial use of electricity in US factories occurred in 1879 when Brush Electric Company installed arc lights in a Philadelphia brush factory
- Thomas Edison's Pearl Street Station, opened in 1882, established America's first centralized power distribution system, serving 85 customers with 400 lamps across one square mile
- Electric motors revolutionized manufacturing starting in 1884 when Sprague Electric Motor Company installed the first standardized system, reducing operating costs by 40% compared to steam power
- By 1920, electric power adoption in US factories reached 78%, with the Northeast leading at 85% electrification rate, while Southern states lagged at 45%
- The transition from steam to electric power resulted in 60% lower operating costs, 75% fewer workplace injuries, and improved efficiency from 30-40% to 85-90%
Conclusion
#The commercial adoption of electricity in US factories marked a revolutionary transformation in American manufacturing history. Starting with arc lighting installations in 1879 and accelerating through Edison's Pearl Street Station in 1882 this technological leap reshaped industrial operations nationwide.
By 1920 electric power had become the dominant force in American manufacturing with adoption rates reaching 78% across the country. The shift from steam to electricity brought unprecedented benefits including enhanced safety reduced operating costs and improved working conditions. This transition stands as a testament to American innovation and entrepreneurship setting the foundation for modern industrial practices.