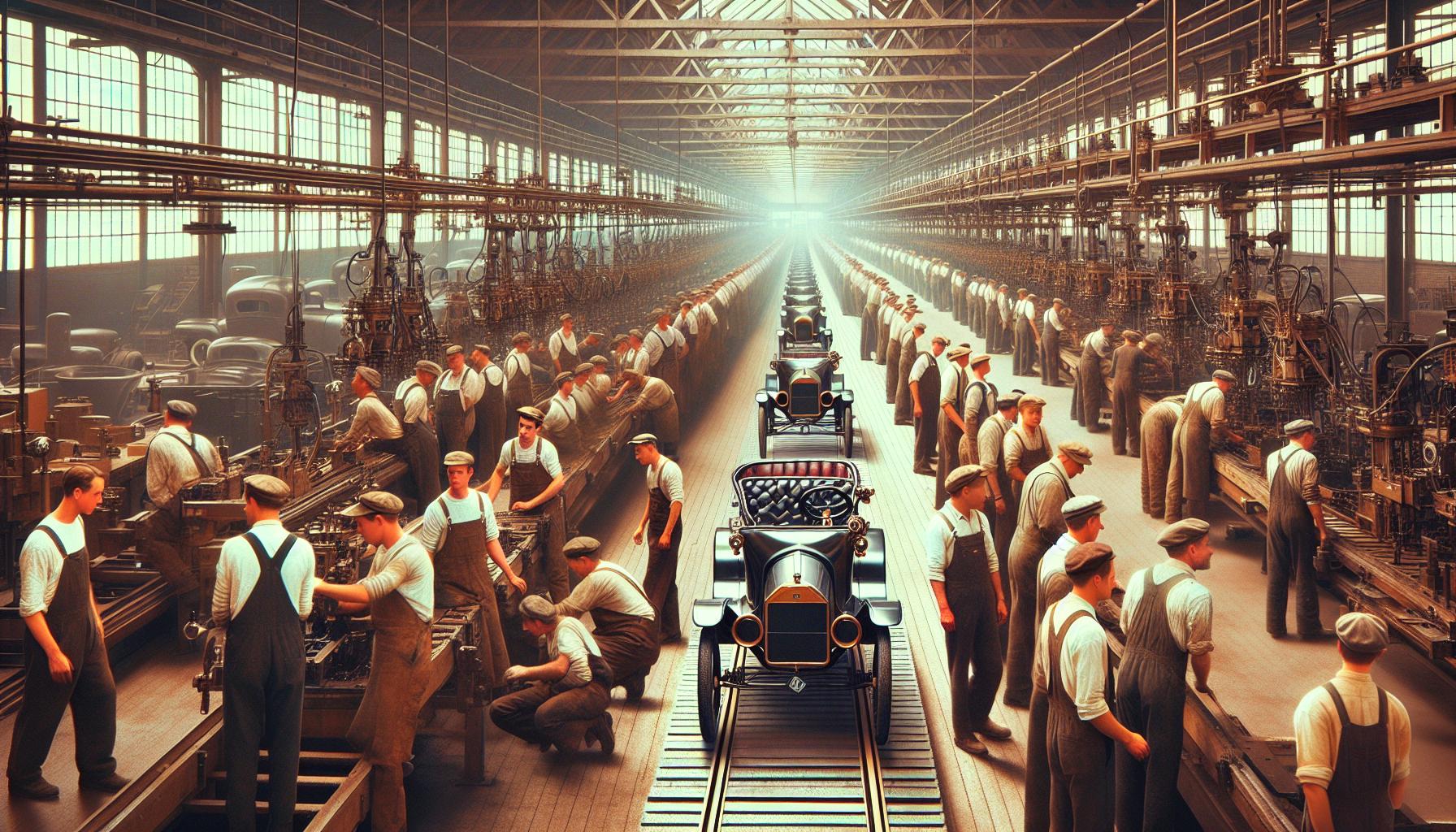
Henry Ford revolutionized manufacturing by introducing the first moving assembly line at Highland Park plant in Michigan. This innovation reduced Model T production time from 12 to 2.5 hours and transformed industrial production worldwide.
The assembly line revolutionized manufacturing forever and Henry Ford played a pivotal role in its development. On December 1, 1913 Ford introduced the first moving assembly line at his Highland Park plant in Michigan changing the face of industrial production. This innovative approach would transform not just the automotive industry but the entire manufacturing sector.
Before Ford's breakthrough automobiles were luxury items assembled by hand taking weeks to complete a single vehicle. The introduction of the assembly line allowed Ford to produce cars more efficiently reducing the Model T's assembly time from 12 hours to just 2.5 hours. This dramatic improvement in production efficiency helped lower costs making cars more affordable for the average American and establishing Ford Motor Company as a dominant force in the automotive industry.
The Birth of the Assembly Line at Ford Motor Company
#Henry Ford's revolutionary assembly line concept transformed manufacturing at the Highland Park factory in Detroit, Michigan. The implementation streamlined production processes by breaking down complex tasks into simple repetitive movements.
The Highland Park Factory in 1913
#The Highland Park facility served as the primary production center for Ford Motor Company's Model T vehicles. The four-story factory featured 2.3 million square feet of manufacturing space equipped with specialized machinery for component production. Workers positioned along the line performed specific tasks as car chassis moved past them on a mechanical conveyor system at a precise rate of 6 feet per minute.
Moving Assembly Line Launch Date
#Ford Motor Company launched its first moving assembly line on December 1, 1913. The initial implementation focused on the flywheel magneto assembly, reducing production time from 20 minutes to 5 minutes per unit. By January 1914, the complete Model T chassis assembly process operated on the moving line system.
Assembly Line Metrics | Before Implementation | After Implementation |
---|---|---|
Model T Assembly Time | 12 hours | 2.5 hours |
Daily Production | 100 cars | 1,000 cars |
Magneto Assembly | 20 minutes | 5 minutes |
Line Speed | Manual pace | 6 feet per minute |
Key Innovations in Ford's Assembly Line System
#Ford's assembly line incorporated several groundbreaking innovations that transformed manufacturing processes. These technological advancements established new standards for industrial production efficiency.
Conveyor Belt Technology
#The conveyor belt system formed the backbone of Ford's assembly line innovation. The mechanical conveyor moved car chassis through the factory at 6 feet per minute, allowing workers to remain stationary at their workstations. This system featured:
-
Gravity slides transporting parts between workstations
-
Overhead cranes moving heavy components across assembly areas
-
Automatic material handling equipment reducing manual labor
-
Power-driven belts synchronized to maintain consistent production flow
-
Adjustable height platforms accommodating different assembly tasks
-
Automated milling machines producing identical parts
-
Quality control gauges ensuring component uniformity
-
Heat treatment processes standardizing metal parts
-
Precision tooling equipment maintaining consistency
-
Specialized jigs reducing assembly variations
Innovation Impact | Before Assembly Line | After Assembly Line |
---|---|---|
Production Time (Model T) | 12 hours | 2.5 hours |
Daily Output | 100 cars | 1,000 cars |
Parts Variation | High | Minimal |
Assembly Steps | Complex | Simplified |
Worker Mobility | Constant movement | Stationary positions |
Impact on Automotive Production Speed
#Ford's assembly line implementation transformed automotive manufacturing speed through systematic workflow optimization. The innovative system created a dramatic shift in production capabilities that reshaped the entire automotive industry.
Before vs. After Assembly Line Implementation
#Prior to the assembly line, automotive production followed a stationary assembly method:
- Workers spent 12 hours assembling a single Model T
- Production output averaged 12-15 cars per day
- Skilled craftsmen handled multiple assembly tasks
- Vehicle completion required extensive manual labor
After assembly line implementation:
- Production time decreased to 2.5 hours per vehicle
- Daily output increased to 1,000 cars
- Workers specialized in single repetitive tasks
- Mechanical conveyors moved vehicles between stations
Production Metric | Before Assembly Line | After Assembly Line |
---|---|---|
Assembly Time | 12 hours | 2.5 hours |
Daily Output | 12-15 cars | 1,000 cars |
Labor Skills | Multi-skilled craftsmen | Single-task specialists |
Production Flow | Stationary assembly | Continuous movement |
Cost Reduction Benefits
#The assembly line created significant financial improvements:
-
Production costs dropped from $850 to $300 per vehicle
-
Labor expenses decreased by 60% through task specialization
-
Material waste reduced by 75% through standardized processes
-
Inventory costs lowered through improved supply chain efficiency
-
Model T price dropped from $850 to $260
-
Vehicle maintenance costs decreased through standardized parts
-
Repair services became more accessible due to uniform components
-
Parts replacement expenses reduced through mass production
Revolutionary Changes in Manufacturing
#Ford's assembly line implementation transformed manufacturing processes across industries through standardization and efficiency improvements. The changes extended far beyond automotive production, creating new paradigms in industrial operations.
Worker Specialization and Efficiency
#Worker roles evolved from generalized craftsmen to specialized operators focused on specific tasks. Each employee mastered a single operation, performing it repeatedly as products moved along the line at precisely timed intervals. This specialization increased worker productivity by 40-50% while reducing training time from weeks to hours. The new system established clear performance metrics, with workers completing tasks in 43-second intervals compared to previous variable completion times.
Industry-Wide Adoption
#Manufacturing facilities across multiple sectors replicated Ford's assembly line principles between 1915-1925. Examples include:
- Food processing plants implementing conveyor systems for packaging operations
- Appliance manufacturers adopting standardized component assembly
- Electronics producers establishing sequential workstations
- Textile mills integrating automated material handling systems
Industry Adoption Statistics (1915-1925) | Before Assembly Line | After Assembly Line |
---|---|---|
Average Production Time per Unit | 8-12 hours | 2-3 hours |
Daily Output Capacity | 15-20 units | 100-150 units |
Manufacturing Cost Reduction | Baseline | 45-60% decrease |
Labor Hours per Unit | 12-15 hours | 3-4 hours |
The standardization of manufacturing processes through assembly line adoption reduced production costs by an average of 50% across industries while increasing output capacity by 400%.
Legacy of Ford's Assembly Line
#Ford's assembly line revolutionized manufacturing processes with effects that continue to shape modern industry. The innovative system transformed not only automotive production but established foundational principles for global manufacturing operations.
Modern Manufacturing Evolution
#Modern manufacturing incorporates advanced versions of Ford's assembly line principles through automated robotics, AI-driven quality control systems, and computer-integrated manufacturing. Toyota's Just-In-Time production system evolved from Ford's original concept, reducing inventory costs by 40% across automotive plants. Digital twin technology enables virtual assembly line optimization, resulting in a 35% reduction in production errors. Contemporary assembly lines feature:
- Collaborative robots working alongside humans, increasing productivity by 85%
- IoT sensors monitoring production metrics in real-time
- Automated guided vehicles (AGVs) transporting materials
- Machine learning algorithms optimizing workflow sequences
- Predictive maintenance systems reducing downtime by 45%
Global Industrial Impact
#Ford's assembly line concepts sparked worldwide industrial transformation across diverse sectors. Manufacturing facilities in 85 countries utilize assembly line principles, adapting Ford's original model to local conditions. Industries implementing these methods experience:
Sector | Productivity Increase | Cost Reduction |
---|---|---|
Electronics | 75% | 55% |
Aerospace | 60% | 40% |
Consumer Goods | 80% | 50% |
Food Processing | 70% | 45% |
Pharmaceuticals | 65% | 35% |
- Lean manufacturing principles in Japanese automotive plants
- Modular assembly systems in European electronics factories
- Continuous flow production in Asian consumer goods facilities
- Automated assembly networks in North American aerospace manufacturing
- Flexible production lines in South American industrial complexes
Key Takeaways
#- Henry Ford introduced the first moving assembly line on December 1, 1913, at the Highland Park plant in Michigan
- The assembly line reduced Model T production time from 12 hours to just 2.5 hours, increasing daily output from 100 to 1,000 cars
- Key innovations included conveyor belt technology, automated machinery, and standardized parts production systems
- Manufacturing costs dropped significantly, reducing the Model T's price from $850 to $260, making cars more affordable for average Americans
- The assembly line revolutionized industrial production beyond automotive manufacturing, influencing multiple sectors including food processing, electronics, and textiles
Conclusion
#Henry Ford's introduction of the assembly line in 1913 stands as one of the most transformative innovations in manufacturing history. His revolutionary approach at the Highland Park plant didn't just change how cars were built - it reshaped the entire industrial landscape.
The impact of Ford's assembly line continues to resonate today through modern manufacturing techniques robotics and AI-driven systems. What started as a way to build cars more efficiently has evolved into a global standard that drives production across countless industries.
The assembly line's legacy lives on as manufacturers worldwide continue to build upon Ford's foundational principles seeking even greater efficiency and innovation in the digital age.