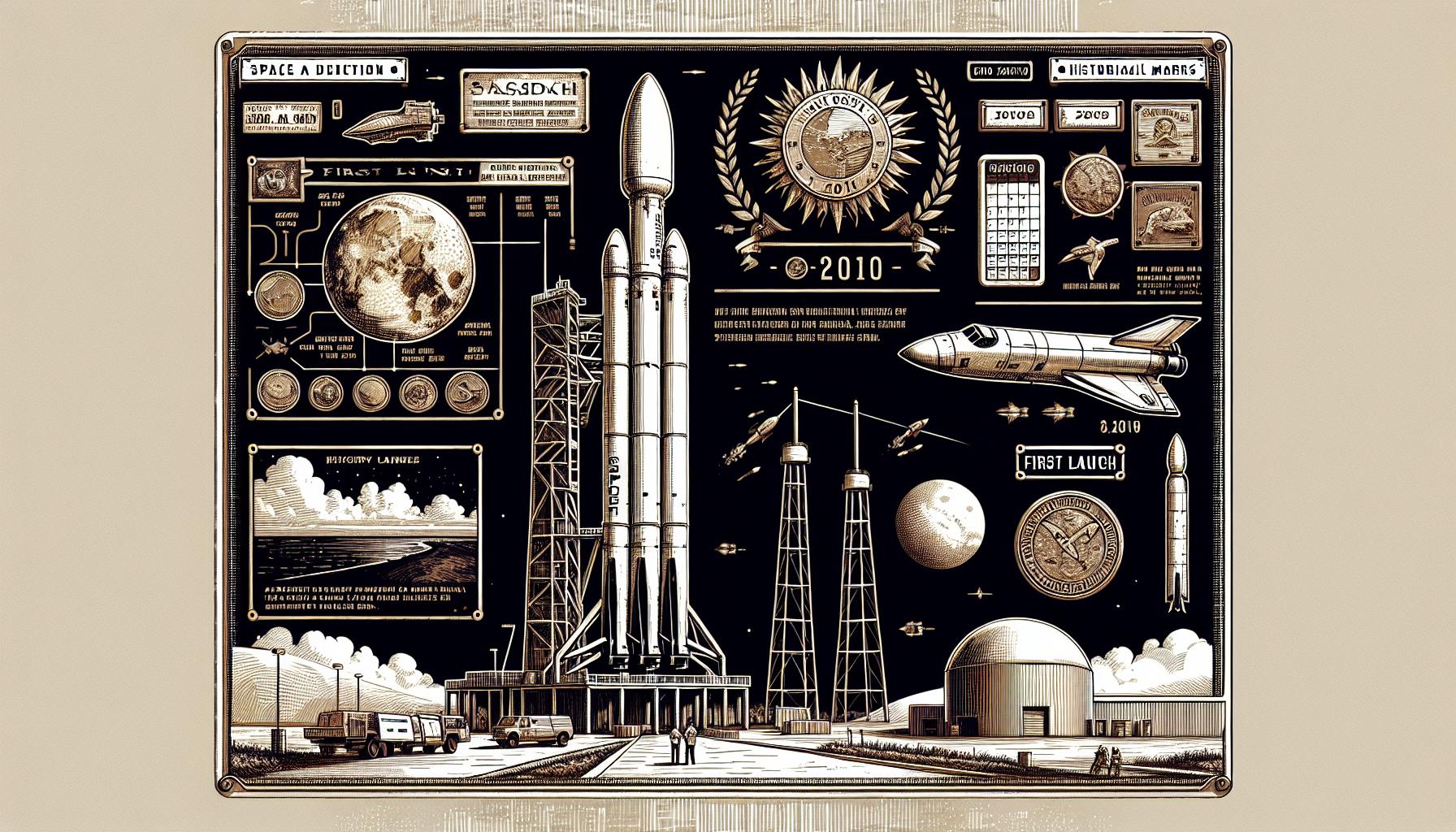
SpaceX's Falcon 9 rocket completed its historic first launch from Cape Canaveral Air Force Station, revolutionizing commercial spaceflight with innovative design and reusability concepts.
SpaceX's Falcon 9 rocket made its historic first launch on June 4, 2010, from Cape Canaveral Air Force Station in Florida. This groundbreaking event marked a significant milestone in private space exploration and set the stage for a new era in commercial spaceflight.
The inaugural flight demonstrated SpaceX's innovative approach to rocket design and reusability - concepts that would later revolutionize the space industry. While this first mission carried a dummy payload designed to simulate a Dragon spacecraft, it proved the rocket's capabilities and laid the foundation for hundreds of successful launches that followed. The Falcon 9's debut flight helped establish SpaceX as a leading force in space transportation and validated Elon Musk's vision of making space travel more accessible and cost-effective.
The Birth of SpaceX's Falcon 9 Program
#SpaceX initiated the Falcon 9 development program in 2005 with a $396 million investment consisting of private funding and NASA's Commercial Orbital Transportation Services program. The rocket's name derives from the Falcon 1 rocket design and its nine Merlin engines in the first stage.
The development timeline included several key milestones:
- Design phase completion in 2006 with the finalization of the basic architecture
- Engine testing program launch in 2007 at SpaceX's Texas facility
- First stage structural testing in 2008
- Full-scale mock-up unveiling in 2009
Key technical specifications of the original Falcon 9 v1.0:
Component | Specification |
---|---|
Height | 47.8 meters |
Diameter | 3.7 meters |
Mass | 333,400 kg |
Payload capacity (LEO) | 10,450 kg |
Engine type | Merlin 1C |
First stage engines | 9 |
Second stage engines | 1 |
Manufacturing innovations implemented during development:
- Vertical integration of production processes
- In-house manufacturing of 85% of rocket components
- Implementation of friction stir welding techniques
- Development of proprietary avionics systems
The program established three primary objectives:
-
Create a reliable medium-lift launch vehicle
-
Achieve rapid reusability of rocket components
-
Reduce launch costs to under $60 million per mission
-
Hawthorne, California: Primary manufacturing facility
-
McGregor, Texas: Engine testing complex
-
Cape Canaveral, Florida: Launch operations center
-
Vandenberg, California: Additional launch site
Development and Testing Phase
#SpaceX conducted extensive development and testing of the Falcon 9 rocket from 2006 to 2010 at multiple facilities across the United States. The rigorous testing program validated the rocket's systems, performance capabilities, and safety measures before its inaugural flight.
Design Innovations
#The Falcon 9's design incorporated several groundbreaking features that set it apart from traditional rockets. Engineers implemented a fuel tank architecture using aluminum-lithium alloy, reducing weight while maintaining structural integrity. The integration of nine Merlin engines provided engine-out capability, allowing the mission to continue even if one engine failed during flight. The proprietary octaweb engine mounting structure enhanced thrust stability and simplified manufacturing processes.
Technical Specifications:
Component | Innovation |
---|---|
Propulsion | Nine Merlin 1C engines in parallel configuration |
Structure | Aluminum-lithium alloy tanks with common dome |
Control System | Triple-redundant avionics |
Recovery System | Grid fins and landing legs for reusability |
Pre-Launch Preparations
#The pre-launch testing phase included 125 engine firings at SpaceX's McGregor facility in Texas. Engineers performed full-duration static fire tests of the first stage in January 2010, validating the integrated propulsion system. The launch team conducted three wet dress rehearsals at Cape Canaveral, testing fueling procedures and launch countdown sequences. Final preparations included payload integration, range safety verification, and comprehensive systems checks completed 30 days before launch.
- Completed engine qualification testing in December 2009
- Performed structural load testing on launch pad 40
- Validated ground support equipment operations
- Certified flight termination system
- Executed communication systems verification
The Historic First Launch
#SpaceX conducted its inaugural Falcon 9 launch on June 4, 2010, at 2:45 PM EDT from Space Launch Complex 40 at Cape Canaveral Air Force Station in Florida. The flight marked a significant milestone in commercial spaceflight history.
Launch Details and Mission Objectives
#The first Falcon 9 mission carried a qualification unit of the Dragon spacecraft, designated DSQU. The flight lasted 9 minutes 38 seconds from liftoff to payload deployment. The primary objectives included:
- Demonstrating first-stage performance through ascent
- Validating stage separation mechanisms
- Testing second-stage engine ignition sequence
- Achieving targeted circular orbit of 250 kilometers
- Gathering telemetry data from 300 sensors
Technical Specifications
#The Falcon 9 v1.0 configuration for the inaugural flight featured:
Component | Specification |
---|---|
Height | 47.8 meters |
Diameter | 3.7 meters |
Mass at Liftoff | 333,400 kg |
First Stage Engines | 9 Merlin 1C |
Second Stage Engine | 1 Merlin Vacuum |
Total Thrust | 4,940 kN |
Fuel Type | RP-1/LOX |
Flight Duration | 9 min 38 sec |
- Wind speeds below 15 knots
- Visibility of 10+ kilometers
- Temperature at 82°F (28°C)
- 60% relative humidity
Impact on Commercial Spaceflight
#The first Falcon 9 launch revolutionized the commercial space industry by introducing reliable, cost-effective launch capabilities. This milestone established SpaceX as a formidable competitor in the global launch market.
Cost-Effectiveness and Reusability
#SpaceX's Falcon 9 reduced launch costs to $62 million per mission, compared to the industry average of $165 million in 2010. The rocket's reusability features enabled:
- Recovery of first-stage boosters through controlled vertical landings
- Refurbishment cycles lasting 4-8 weeks between flights
- Cost reduction of 30% for customers choosing flight-proven boosters
- Multiple reuses of a single booster, with one achieving 15 successful launches
Cost Comparison (2010) | Price per Launch |
---|---|
Traditional Providers | $165 million |
Falcon 9 | $62 million |
Reused Falcon 9 | $43 million |
This economic model transformed space access by:
- Creating competition in the launch services market
- Enabling smaller companies to afford satellite deployment
- Reducing insurance costs through demonstrated reliability
- Establishing new industry standards for launch vehicle economics
The implementation of reusable technology sparked industry-wide changes in rocket design, manufacturing processes, pricing structures. These innovations led to a 300% increase in commercial launch activities between 2010-2020.
Modern Legacy of the First Flight
#The inaugural Falcon 9 launch established technological benchmarks that transformed space transportation. SpaceX's achievements since 2010 include:
- Completed 250+ successful orbital launches
- Achieved 200+ successful booster landings
- Reduced launch costs by 75% compared to traditional providers
- Established rapid reusability with 15 reuses per booster
- Created 40,000+ aerospace manufacturing jobs
The Falcon 9's innovations sparked industry-wide advancements:
- Reusable rocket technology adoption by competitors like Blue Origin
- Standardization of vertical landing systems
- Implementation of automated flight control systems
- Development of lightweight composite materials
- Integration of machine learning in flight operations
The economic impact reflects the mission's lasting influence:
Metric | 2010 | 2023 |
---|---|---|
Global Launch Market Value | $5.4B | $19.8B |
Average Launch Cost | $165M | $62M |
Annual Commercial Launches | 23 | 87 |
Private Space Companies | 12 | 375+ |
Industry Employment | 48,000 | 195,000 |
The first Falcon 9 flight's technical architecture continues to influence modern rocket design:
- Nine-engine configuration for redundancy
- Aluminum-lithium alloy structures
- Subcooled propellant systems
- Autonomous flight termination
- Propulsive landing capabilities
These innovations established operational standards across the commercial space sector, leading to accelerated development of new launch vehicles, expanded satellite deployment capabilities, and increased access to space-based services.
Key Takeaways
#- SpaceX's Falcon 9 rocket made its historic first launch on June 4, 2010, from Cape Canaveral Air Force Station in Florida
- The development program began in 2005 with a $396 million investment, combining private funding and NASA's support
- The original Falcon 9 v1.0 featured nine Merlin 1C engines and could carry 10,450 kg to low Earth orbit
- The inaugural flight lasted 9 minutes 38 seconds and successfully demonstrated the rocket's capabilities with a dummy Dragon spacecraft payload
- The Falcon 9 significantly reduced launch costs to $62 million per mission, compared to the industry average of $165 million in 2010
- Since its first launch, SpaceX has completed over 250 successful orbital launches and revolutionized the space industry with reusable rocket technology
Conclusion
#The first Falcon 9 launch on June 4 2010 revolutionized the space industry and set new standards for commercial spaceflight. SpaceX's innovative approach to rocket design reusability and cost reduction has transformed space access making it more affordable and accessible than ever before.
The success of this inaugural flight laid the foundation for over 250 successful missions 200 booster landings and a remarkable 75% reduction in launch costs. Today's thriving commercial space sector with its numerous private companies and expanded launch capabilities stands as a testament to the groundbreaking achievements of that first Falcon 9 mission.